Bau
So dann geht es jetzt los...
Zuerst waren die Rippen für die Flügel zu erstellen.
Hierzu wurden die oberen und unteren Gurte in eine Spezial-Badewanne eingelegt, damit sie weich werden konnten.
Ansonsten hätte man beim Biegen der Kieferleisten um enge Radien kein Spaß, weil die Leisten dauernd brechen.
In der Zwischenzeit wurden auf die Baubretter die geplotteten Rippenpläne aufgespannt, eine Folie drübergezogen und mit Nägeln
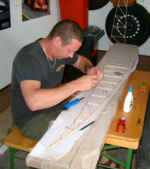
(deren Köpfe abgeknipst wurden) die Außenkonturen abgenagelt. In die Nagelformen die weichen Leisten eingelegt, von innen
auch mit ein paar Nägeln fixiert. Jetzt begann der Spaß! Fachwerk bauen...
Bei der Flugsau waren es 26 Rippen, wobei nur 18 gleich groß waren. Es wurden für alle Rippen ca. 200 m Kieferleiste verarbeitet.
Wenn man noch bedenkt, dass die meisten Stückchen nur um die 10 cm lang waren und pro Leiste zwei Gehrungsschnitte nötig wurden...
und auf jeden Knotenpunkt noch von oben und unten ein 0,4 mm dickes Sperrholz als Verstärkungen aufgeleimt wurde...
Dann wird es verständlich, dass es nicht einfach war, die Helfer immer wieder von der Sache zu begeistern.
Dann hieß es, die Hauptholme zu bauen. Dabei ist gutes Holz sehr wichtig, es muss zum einen astfrei sein und je enger und gleichmäßiger
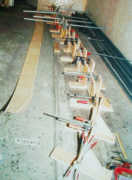
die Maserung ist, desto höher ist die Festigkeit. Es wurde mit dem E216 ein Profil gewählt, das bei einer Tiefe von 2,10 m eine Höhe
von 21,8 cm hat. Der Holm ist als doppel-T Träger ausgeführt, das bedeutet, es wurde eine 1,5mm starke Sperrholzplatte als Steg genommen,
oben und unten jeweils zwei 15 × 15 mm starke Hartholzleisten links und rechts dagegen geleimt. Wegen dem gesamt Gewichts verdünnen sie sich
nach außen stark. Jeder der Holmgurte muss (innen) eine Last von 4,4 KN aufnehmen. (Das entsprichte ca. 440 Kg). Für den Leimvorgang, muss
für jeden Holm eine eigene Hehling gebaut werden, damit der Holm genau die Form bekommt, die er haben soll und damit viele große und
schwere Schraubzwingen genügend Pressdruck erzeugen können.
Jetzt wurde es eng. Wo sollten die Tragflächen gebaut werden? Zuerst musste der Keller im Elternhaus herhalten. Doch hat sich die
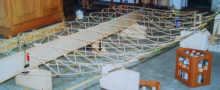
Befürchtung schnell bewahrheitet, dass die montierte Tragfläche "fast" nicht aus der Tür ins Freie gepasst hätte. Es ist aber bei dem Versuch nur eine Rippe
abgebrochen, die wir erst eben angeleimt hatten. Bei dem Anleimen der Rippen wurde natürlich auf die Verwindung geachtet, die die äußeren
Rippen haben sollten. Durch die Verkleinerung des relativen Anstellwinkels in Bezug zum Rest der Tragfläche ist es gewähleistet, dass die
Strömung erst am inneren Teil der Tragfläche abreißt. Damit ist ein gutmütiges Abrissverhalten ermöglicht, weil der Hebelarm
von Rumpfmitte bis zur abgerissenen Strömung kleiner ist, als wenn die Strömung außen abreißt.
Bei dem ersten Test des Hauptholms hatte ich eine erschreckende Endeckung gemacht. Der Steg beult!!! Ich hatte den mittleren Teil des
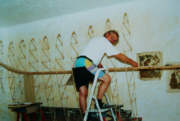
Holms auf den Boden gelegt und mich in dem Bereich des "V"- Knicks auf ihn gesetzt. In dem Moment, wenn der Holm ganz außen angehoben wird und
versucht mich vom Boden zu heben, dann knickt die nur 1,5 mm Dicke Sperrholzplatte seitlich aus. Um das zu verhindern, wurden in Abständen von ca. 20 cm
(Holmhöhe) kleine Leistchen 3×4 mm Querschnitt eingebaut, die das Beulfeld in viele fast quadratische Beulfelder unterteilen. Damit hat man mit einem
Mehrgewicht von ca. 50 g die Tragfähigkeit des Holms um 60 bis 70 Kg angehoben.
Jetzt kommt der interessante Teil. Das Beplanken des Nasenbereichs der Tragflächen. Wie erreicht man einen Biegeradius von ca. 2 cm, ohne
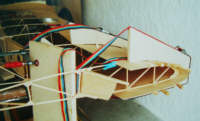
dass das Sperrholz bricht? Wässern ist die Lösung. Dazu wurde das 1,5 mm dicke Sperrholz immer von beiden Seiten feucht gemacht und eine Vorrichtung
gespannt, die bei jedem Vorgang etwas enger gedreht wurde. Dann wurden die im Vorfeld auf Maß geschnittenen, am Rand geschäfteten und eingeleimten Beplankungs-
platten mit Hilfe von negativen Schablonen, Keilen, Nägeln und Spanngurten aufgezogen. Jedes Feld durfte richtig lange aushärten, weil
in der Zeit die nächste Beplankungstafel vorbereitet wurde.
Da die Beplankung aus Gewichtsgründen nicht bis zum Hauptholm ging, hatte ich aus 10×10 mm Balsaleisten ein Fachwerk vom oberem zum
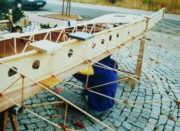
unteren Beplankungsende gebaut. Dadurch war die Torsionskiste erst eine "Kiste" und konnte ihrer Aufgabe gerecht werden. Gleichzeitig wurden auch noch
diagonale (von oben gesehen) Träger eingebaut, die die gesammelten Kräfte aus der Torsionskiste an den Hauptholm abgeben. Die Löcher
im Steg und die Ver-
dünnung der Gurte vom Hauptholm brachten eine Gewichtsersparniss von ca. 400 g pro Tragfläche. Das ist bei einem Gesamtgewicht von ca. 9 Kg pro Tragfläche eine ganze Menge.
Im vorderen Bereich waren die Tragflächen schon fast fertig, hinten waren bisher nur die Rippen, die dort herumwackelten. Darum wurde eine
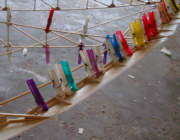
Endleiste erstellt, die zum einen die Rippen miteinander verband und auch der Bespannung festen Halt geboten hat. Die Endleiste war ca. 7 cm breit und,
damit sie nicht zu schwer wurde, innen hohl. Hergstellt wurde sie aus 1 mm bzw. 0,8 mm dicken Sperrholz, das mit Balsa- Stegen und Leimeckenverstärkungen
versehen war. Denn damit war gesichert, dass die Endleiste auch Biege- und Torsionskräfte aufnehmen konnte, ohne zu beulen.
Die Tragflächen wurden so gebaut, dass sie zum Montieren nur zusammengeschoben werden mussten und die so genannten Holm-
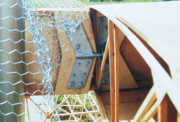
verbinder ineinander einrasteten. Diese Eisenteile waren auf Verstärkungen aus Eichenholz auf den Steg geleimt und mit vielen M3 Schrauben gesichert.
Durch diese Verbindungsart konnte auch gewährt werden, dass die Biegekräfte im Hauptholm blieben und sich der Linke am Rechten und umgekehrt
abstützte. Der Rumpf brauchte nur noch die reine Auftriebskraft aufnehmen. Und dies geschah auch wieder mit Alu-Taschen, die mit diagonalen
Eisenbändern am Alurohr-Tragesystem vernietet waren.
Wenn die Tragfläche schon so aussehen soll wie bei einem Vogel, dann müssen auch die Randfedern hochgebogen sein. Deshalb wurden an
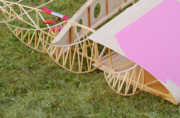
der äußersten Rippe quer kleine gebogene Fachwerk- Rippen angebaut, die dünne (1×1 mm) Längsgurte getragen haben. Diese wurden ganz normal
bespannt. Bei der Formgebung wurde darauf geachtet, dass das Profil der letzten Rippe weiterlief und einfach nur langsam nach oben gedreht wurde, bis es am
oberen Rand auf die Dicke "Null" ausgelaufen war. Von oben gesehen ergab der hochgezogene Randbogen eine elegante Ellipse und die Spannweite betrug damit genau 8,98 m
(also kleiner als 9 m). So war auch das Red-Bull Regelement eingehalten.
Womit bespannt man eine Tragfläche, die als oberstes Gebot leicht, aber auch günstig und luftundurchlässig sein soll? Seide ist leicht aber
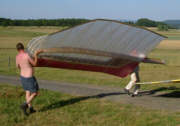
viel zu teuer. Dünner Leinenstoff ist nicht ganz so leicht, sehr luftdurchlässig und muss daher mehrfach mit Farbe versiegelt werden, was ihn noch
schwerer macht. Japanpapier ist leicht, aber sehr empfindlich. Deshalb habe ich Plastik-Bau-Folie gewählt. Nachdem die Probleme der Befestigung auf den Holzrippen
gelöst waren, ging das Bespannen mit 6 Helfern gut von der Hand. Die Folie war super stramm, weil wir sie im erwärmten Zustand verarbeitet hatten,
sehr robust und einfach zu reparieren.
Es ist doch wirklich gut, wenn man einen Künstler als Vater hat. Der ist dann für die Farbgestaltung etc. verantwortlich. Ob er sich gegen die
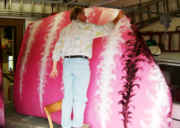
Ehre (Arbeit) gewehrt hat? Das verraten wie hier lieber nicht. Es kann ja gut sein, dass man ihn noch einmal braucht...
Die Farben wurden extra angemischt (so ein Rosa ist nicht unbedingt die am meißten verkaufte Farbe) und in vielen dünnen Lagen aufgetragen, weil
die Bespannung die Farbe nur sehr schwer angenommen hat. Und einfach dick drauf klatschen war streng verboten, denn Farbe ist nur unnötiges Gewicht...
Wenn auch andere behaupten, ohne eine schöne Lackierung bräuchte man auch gar nicht bei dem Red-Bull Wettbewerb teinehmen.
Bau des Rumpfes
Der Rumpf sollte mit Ausnahme des Höhenleitwerks nur sich selbst tragen. Daher ist es möglich gewesen ihn sehr leicht mit Hilfe von Fachwerkspannten und
Längsgurten zu konstruieren.
Nachdem alle Rippen erfolgreich gebaut waren, konnte die gelernte Handwerkskunst gleich bei den Spannten für den Rumpf noch einmal
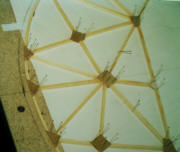
angewandt werden. Diesmal waren 10 Spannten zu bauen, deren Rundungen allerdings noch viel größer (als bei den Rippen) waren. Die obere Hälfte beschreibt eine relativ
flache Ellipse, während die untere Ellipse sehr bauchig, schon fast rund war. Es ist klar, dass hier jeder Spannt eine andere Größe
und Form hat... Der kleinste Spannt ist gerade mal 23 × 10 cm groß und hat auch eine gebogene Kieferleiste von 3 × 4 mm
als äußeren Gurt! Dazu braucht man viel Geduld beim Biegen und in der Regel auch einen zweiten Versuch...
Dann wurden alle Spannten innen vorübergehend mit Styropor ausgefüllt, die Achsen der Ellipsen eingezeichnet und im Achsen-
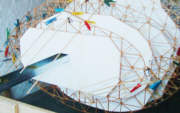
Schnittpunkt eine Aussparung für ein Stahlträger vorbereitet. An dem Träger selbst wurden die Positionen der Spannten markiert und dann der Reihe nach "aufgefädelt".
In den Quadranten wurden die ersten Längsleisten angeheftet und die Spannten endgültig ausgerichtet. Jetzt konnten alle Längsleisten angeklebt werden und Verstärkungen
in Form von Fachwerksverbund zwischen den Längsleisten eingebaut werden. Die Sonderzonen mit dem oberen und unteren Ausschnitt (für den Piloten) wurden besonders verstärkt.
Mit Hilfe von dicken aber dünnwandigen Alurohren wurde eine vernietete Tragkonstruktion im Rumpf geschaffen, an welcher der Pilot sich wie im
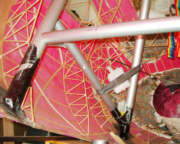
Drachen einhängen kann. Von diesem Einhängepunkt wurden die Hauptkräfte direkt zu dem Anschlusspunkt der Tragflächenholme geleitet. Dann galt es auch noch
Haltepositionen zu schaffen, an der der Pilot die gesamte Maschine tragen und steuern kann. Der Anschluss an die Holzspannten/ Längsträgerkonstruktion erfolgte mit Hilfe
von Sperrholzverstärkungen an die die Alurohre mit Kohlefaser geklebt wurden. So gesehen musste die Rumpfschale nur sich selbst und das Leitwerk tragen.
Der nächste Schritt war wieder künstlerischer Natur: Es ging darum die Schnauze, Ohren und die riesigen Augen zu modellieren. In
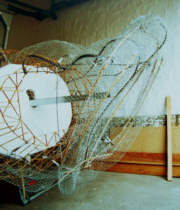
Anbetracht der knappen Zeit bis zu dem Red Bull Flugtag war mein Plan, diese Elemente aus Styro- Schalen mit Papierüberzug zu konstruieren nicht realisierbar.
Darum wurden mit einem feinen Maschendraht die Formen modelliert und mit dünnen Holzleisten oder Blechstreifen an der einen oder anderen Ecke verstärkt.
Anschließend mit Pappmaschee beidseitig verkleidet. Die Pappmascheeaktion musste einige Male wiederholt werden, bis eine ausreichende Festigkeit gegeben war.
Ich muss schon gestehen, dass es hin und wieder vorteilhaft ist, wenn die Eltern künstlerisch begabt sind. So kann man ihnen relativ einfach "einreden" dass ihnen so ein
Job viel Spaß macht. Somit hat man selbst wieder Zeit um z.B. die mit Blechstreifen verstärken Hauptholm-Alutaschen an das Rohrsystem zu nieten...
Vorne herum hatte die Flugsau mit diesen Arbeitsschritten schon eine recht passable Figur abgegeben. Hinten sollte es genauso werden.
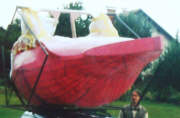
Darum habe ich zwei zusätzliche Rippen für das Höhenleitwerk gebaut. Die wurden am Ende des Rumpfes genau ausgerichtet und mit dem Rumpf fest verklebt. Anschließend
die Rundungen des Rumpfes elegant in die spätere Kontur des Höhenleitwerks gestrackt. Somit gab es keine Kanten, sondern nur noch einen sauberen Übergang zwischen
Rumpf und Leitwerk. Gleichzeitig habe ich mir etwas Spiel gelassen um das Leitwerk vom Anstellwinkel noch variieren zu können, falls die Probeflüge eine EDW- Änderung
notwendig werden lassen.
So kann es aussehen, wenn wieder mal der "Meister Klecksel" am Werk war. Der schielende Blick war gewollt. Es sollte einfach etwas lustiger
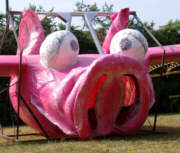
aussehen. Leider hatten wir nicht daran gedacht, das eine kurzsichtige oder schielende Flugsau evtl. den perfekten Flugweg nicht richtig erkennen kann...
Süß sieht sie ja trotzdem aus!
Bau des Höhenleitwerks
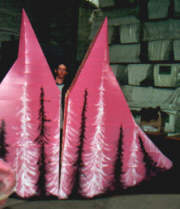
Hinten am Rumpfende ist es äußerst wichtig leicht zu bauen. Jedes Kilo zuviel müsste mit 4 Kg an der Nase ausgeglichen werden. Spart man also ein Kg ein, heißt dass,
das man im Endeffekt 5 Kg leichter gebaut hat.
Zur Umsetzung dieser Forderung müsste man ein ganz einfaches rechteckiges Leitwerk bauen.
Das Höhenleitwerk sollte aber im Grundriss dem Schwanz eines Vogels ähnlich sein. Daraus resultiert entweder wieder mehr Gewicht, oder eine sehr unkonventionelle Bauweise.
Angefangen wurde mit den Rippen des Leitwerks. Da das symmetrische Profil NACA 0006 zum Einsatz kam, und keine Verwindung eingebaut
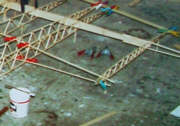
werden sollte, war jede Rippe in einer anderen Höhe vom Boden aus gemessen zu platzieren. Das Leitwerk bekam einen Hauptholm, der jedoch (wegen der Teilbarkeit und Montage)
herausnehmbar war. Ein zweiter, deutlich weiter hinten montierter Hilfsholm lief über die gesamte Spannweite durch.
Die vordere (geschwungene) Kante wurde durch eine 3 fach abgeknickte Linie angenährt. Gebaut wurde sie aus 1 mm starken Sperrholz, das in
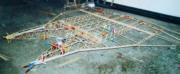
Streifen à 3 mm bis zur Mittellage eingeritzt wurde. Damit ließ es sich vorsichtig um die Nase des Profils ziehen. Damit später wieder Festigkeit in diese sehr labile Nasenleiste
kommen konnte, wurden die Längsschnitte dick mit Ponal eingestrichen, damit das Sperrholz wieder eine Einheit wurde.
Der nächste Schritt war die Versteifung des gesamten Leitwerks. Dazu wurden quer zur Flugrichtung in halbwegs konstanten Abstand Leisten
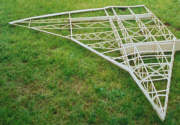
über die Rippen geleimt, die eine Fachwerkaussteifung bekommen hatten. Somit sind viele "Hilfsholme" entstanden, die das ehemals sehr wacklige Leitwerk in eine recht steife
Konstruktion verwandelt hatten. Der positive Nebeneffekt war der, das die Bespannung jetzt deutlich mehr Auflagerpunkte hatte und nicht mehr durchhängen bzw. flattern konnte. Bespannt
wurde es mit einer sehr dünnen Plastikfolie. Direkt vor dem Bespannen wurde sie mit einem Warmgebläse erwärmt und dann ganz schnell auf die Holzkonstruktion gespannt.
Ich wollte es fast selbst nicht glauben, aber das Leitwerk hat bei einer Länge von 2,60 m und einer Spannweite von 3,60 m nur
2 Kg Gewicht. d.h. etwas über 400 g pro
m
2 Fläche.
Das ist Leichtbau!!!
wird fortgesetzt!!!
letzte Aktualisierung
am: 06.07.2006